The choice of the ideal insert for the turning processing is the first step towards optimising the production process, this passes through the evaluation of some primary and other secondary parameters that are also important.
- Machining profile for the choice of the insert shape and attachment angle
- Insert geometry according to the type of machining, roughing, medium-finishing or finishing
- Size of the insert
- Corner radius
- Substrate quality and coating
These parameters should be evaluated with the material that you have to work, the rigidity of machining.
1 - Machining profile and attachment angle
The figure in Tab.1 below identifies the ideal insert shape according to the profile that have to be executed, combined with Tab.2 which identifies the attachment angle or recording that affect the chip formation.
Chip thickness is directly proportional to the angle of attachment, if the angle of attachment increases consequently the thickness increases but the width decreases, this cutting condition also affects the direction of the chip output.
Tab.1
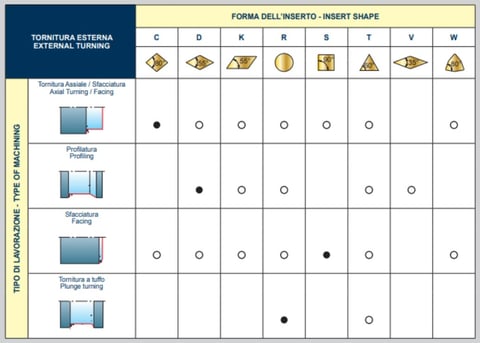
Tab.2
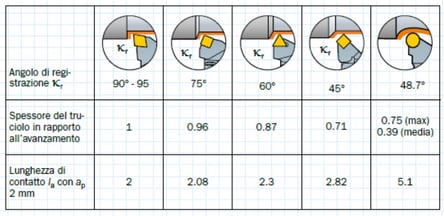
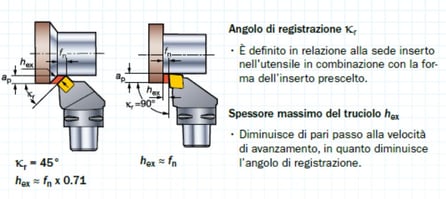
2 - Insert geometry
The insert geometry must be chosen according to the machining required
ROUGHING:
- The cutting edge robustness and the big corner radius allow cutting depth and high feeds, this type of machining requires a high cutting force
MEDIUM-FINISHING:
- Inserts for this type of machining are the most used because they allow feeds and cutting depth that go from roughing to semi-finished
FINISHING:
- The sharp cutting edge praparation and the corner radius suitable for the depth of the pass ensure low shear forces and a good surface finish
For an optimal chip control, the insert’s field of application must be within the graphs in the catalogue, see example Tab 3.
Tab.3
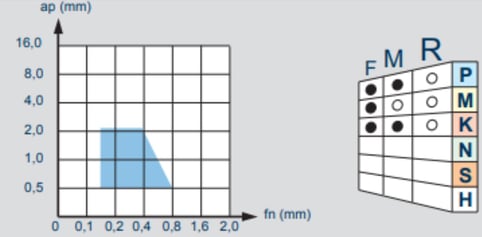
3 - Size of the insert
The type of machining also affects the size of the insert, this must be chosen according to the depth of "ap" pass and the type of insert used.
In Tab.4 there is the guideline for a correct robustness proportion of the cutting edge and an insert economy.
Tab.4
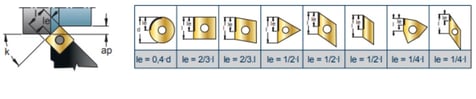
4 - Corner radius insert
Another important factor to evaluate which is often underestimated is the corner radius of the cutting edge, for a correct application this should generally not be less than 2/3 of the "ap" cutting depth. In addition, factors such as surface finish, chip formation and cutting edge strength are linked to the insert radius.
Generally the small radius has a weak cutting edge and is used for finishing operations with low cutting depth, where there are vibration problems and a better chip control. On the contrary, the large radius is a symbol of the sharpness of the cutting edge, great cutting depths and high feeds, this causes increased cutting forces and therefore risk of vibration.
In Tab.5 there is an extract of the SAU catalog where the maximum feeds recommended are indicated according to the insert radius and theoretically approximate (but sufficiently reliable) the roughness that is obtained in relation between radius insert "rɛ" and feed "fn".
Tab.5
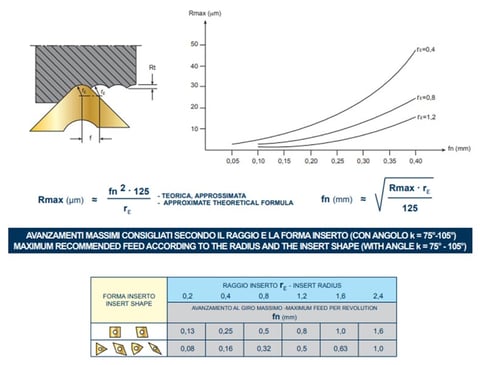
5 - Substrate quality and coating
Other factors that determine the insert choice to be used for machining are
- Material to work (steel, stainless steel, cast iron, non-ferrous, heat-resistant alloy, hard steel)
- Material condition (rolled, forged, printed, exc..)
- Machining type (roughing, medium-finishing, finishing)
- Working conditions (good, medium, difficut)
Substrate or hard metal base, coating with PVD or CVD technologies and cutting edge geometry, create the ideal combinations for the processes required.
In Tab. 6,7,8,9 there is the correct sequence to identify the insert and the application parameters.
Tab.6
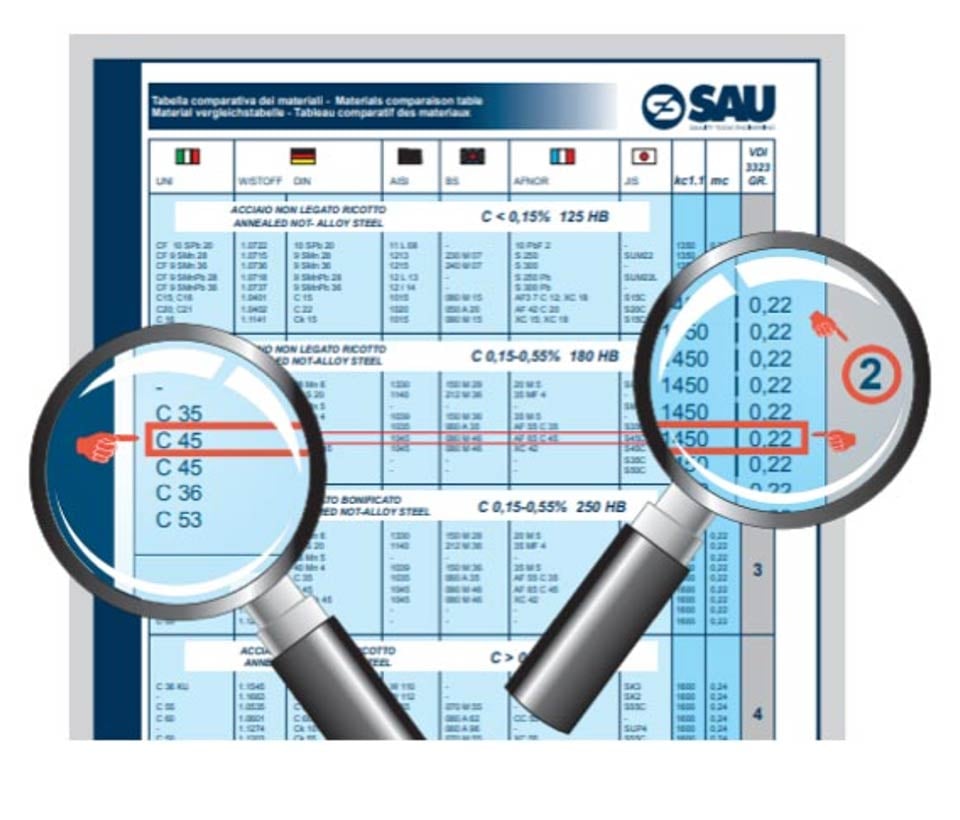
Tab.7
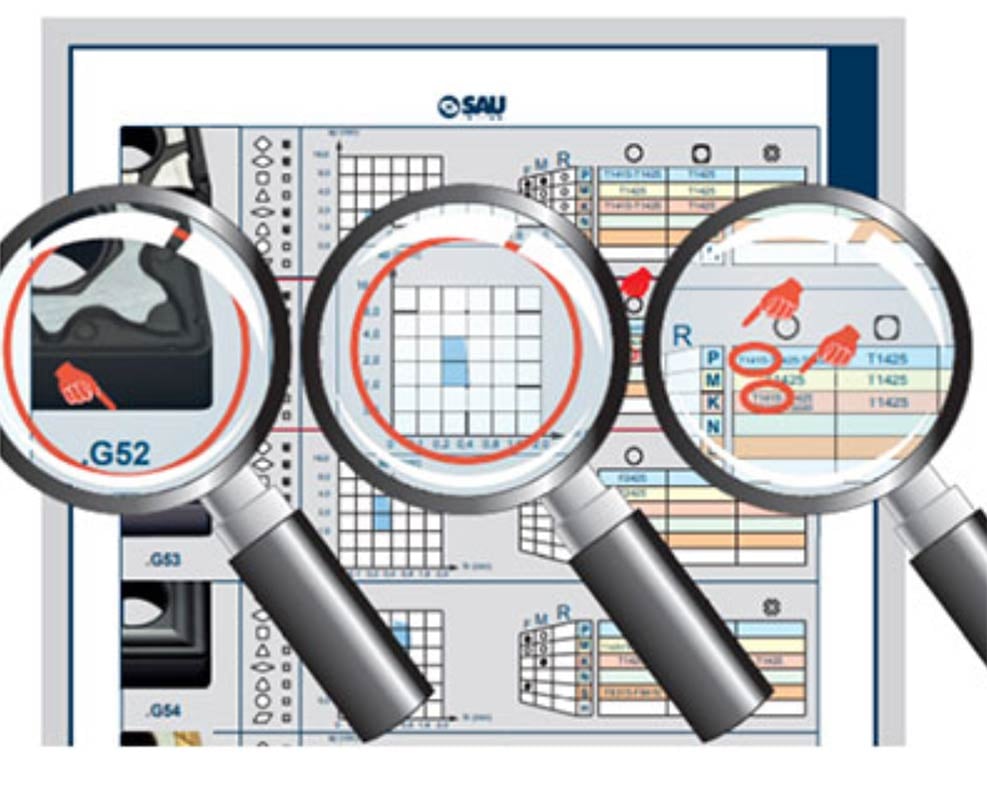
Tab.8

Tab.9
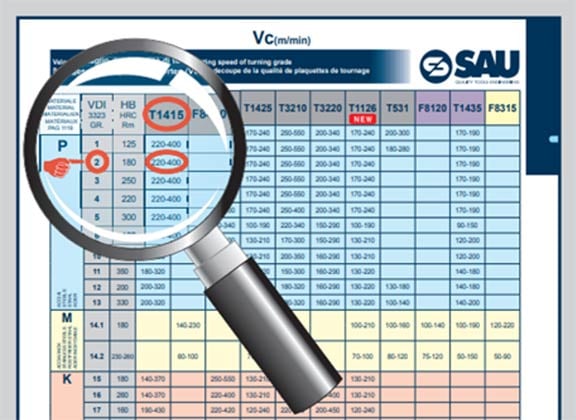