In industrial machining cycles, the correct fixing of the clamping screws and inserts on the tools is a crucial aspect to avoid movements and breakage.
From correct use to timely replacement of screws and inserts, there are many factors that directly affect the operation and durability of the tools used, with consequences on the management of production cycles.
Let’s see together how to better manage these activities.
The importance of precision in fixing inserts
The correct attachment of the inserts to the tool requires care and precision.
Improperly positioned or tightened screws can cause harmful micro movements, chipping or even tool breakage.
It is essential to use the screws recommended in the catalog by the manufacturer, apply the precise load and adhere to the tightening specifications to ensure stability and durability.
The correct fixing is a critical aspect: a screw without the right draw can be damaged quickly, preventing the correct operation of the tool.
In any case, any screw has a life cycle and with the passage of time and wear, it becomes necessary to replace it. We must also consider this aspect.
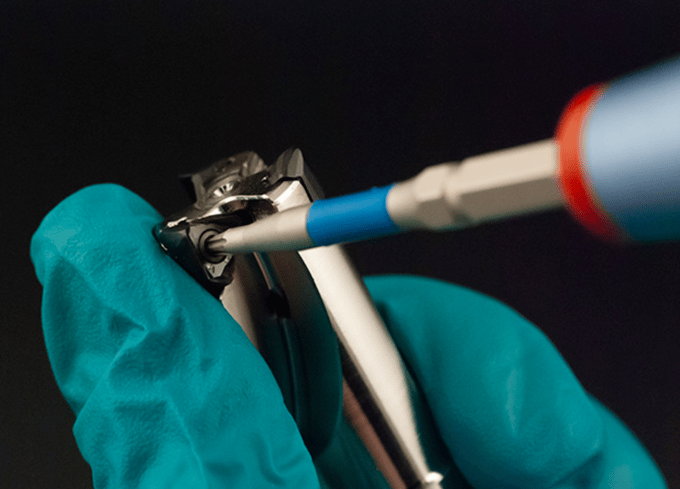
The importance of the correspondence between screw and insert
Each cutter requires a specific screw according to its characteristics.
Although two tools may look similar, the screw head may vary, affecting their correct fastening. It is crucial to choose the correct screw, following the precise indications provided on tools and catalogs.
Adjusting the tightening torque, however, is not always easy and a torque screwdriver is very useful to speed up the tightening, thanks to the self-regulation allowed by this tool.
The choice of the screw code
As we have mentioned, the selection of the suitable screw for the tool in use is a fundamental step to ensure a safe and reliable fixing.
Each tool, depending on its characteristics, requires a precise correspondence with the screw that holds it in place, and this correspondence is determined by a number of factors, each of which contributes to the overall efficiency of the gear and operator safety:
- 1. Technical Specifications: Each tool has unique technical requirements, such as diameter, thread type and length. The choice of screw must comply with these specifications to ensure a precise and safe fixing.
- 2. Clamping force: LeThe specification tables provide information on the clamping force required for each type of screw in relation to the tool in use. This helps operators to precisely adjust the tension applied during fixing, avoiding both excessive and insufficient tightening.
- 3. Insert compatibility: Each insert has different attachment requirements. The choice of screw should consider not only the tool itself, but also the insert that is applied. The correct correspondence between screw and insert ensures a perfect fit, minimizing the risk of unwanted movements or breakage.
- 4. Type of head: The type of screw head and the fixing tools used can vary greatly, although they may look similar. Proper screw selection ensures that appropriate tools can be used for precise and trouble-free fastening.
- 5. Materials and characteristics of the Tool: The nature and properties of the tool, such as its resistance to heat or vibration, influence the choice of screw. A suitable material and proper application can prevent seizing or damage to the tool.
- 6. Specifications for clamping: The tables of tightening specifications serve as a guide for operators and allow to adopt a precise methodology in fixing the screws.
These indications are the result of extensive testing and provide specific values for each combination of tool and screw, ensuring correct and safe application.
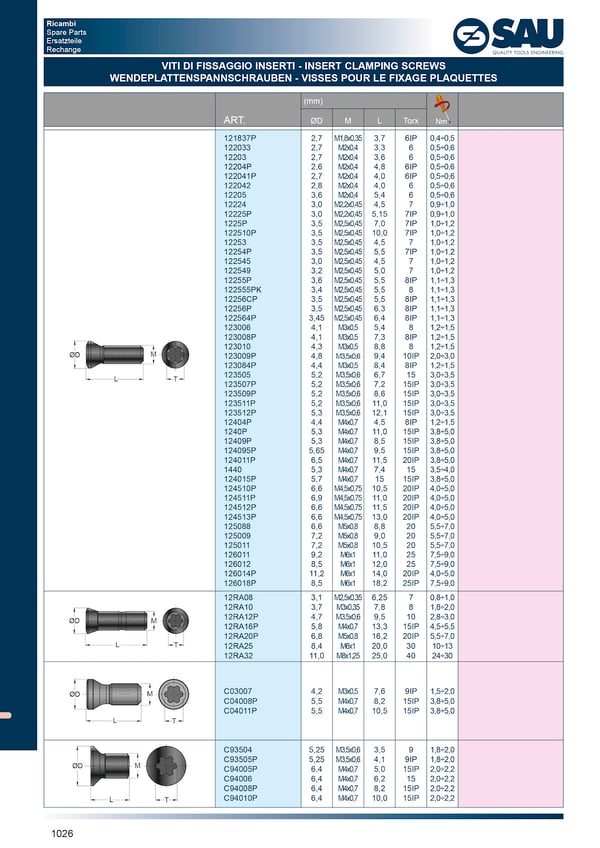
Grease to prevent seizure
An underrated support is the use of a grease specific to the tool screws.
Applied correctly, this grease acts as a barrier against seizure, ensuring correct closure of the inserts even under conditions of vibration or high temperatures. In fact, these industry-specific greases protect the screws from very high temperatures that rise during machining and, helping to maintain the optimal performance of the tools over time.
DINAPLUS®: SAU torque screwdriver
SAU has been manufacturing and distributing tools for the manufacturing world in various sectors for more than 40 years, as well as being a point of reference for the design and manufacture of custom-made special tools.
For a correct management of the screws in the inserts’s fixing, we recommend the use of DINAPLUS®, the torque screwdriver that, thanks to a self-regulation system, eliminates the need to control the tightening torque.
This not only simplifies the work of the operator, but also ensures correct fixing without requiring continuous manual intervention.
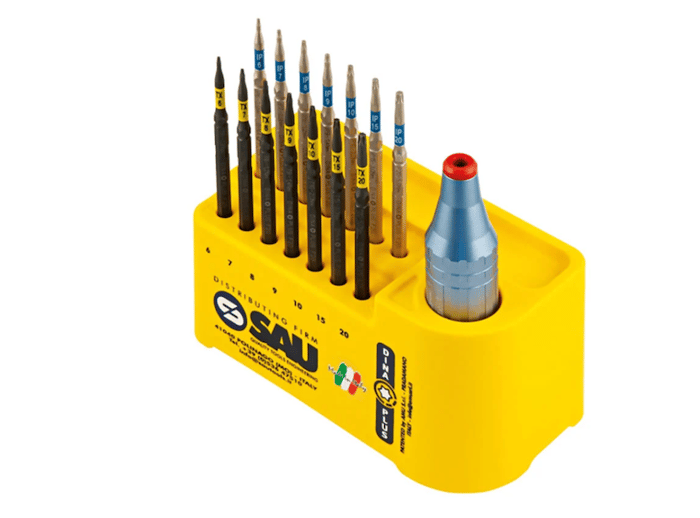
Advantages in using DINAPLUS®
Let’s see the advantages in using DINAPLUS® torque screwdriver from SAU:
- Quick use
- Immediate adjustment
- Auto-setting
- Better tightening of the screw
- Use for multiple screws (TORX® e TORX® PLUS, ecc.)
- Easier unscrewing and no clutch problems
- Optimization of the clamping force
- Greater life of the screws
Discover more about DINAPLUS® visiting this page.
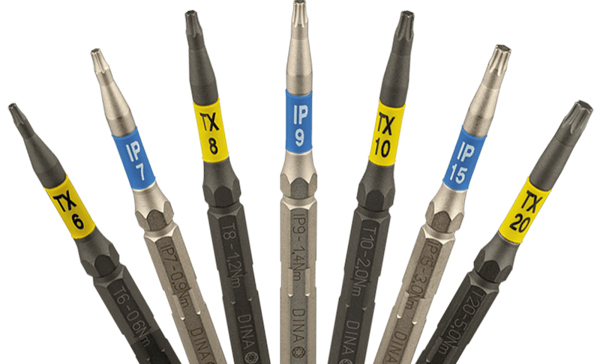
Conclusions
The careful selection of the screw according to the specifications of the tool, the clamping tables and the characteristics of the insert is essential to ensure optimal operation of the tools and safety in the workplace.
Choosing the right screws, paying attention to the mounting details, using a torque screwdriver such as DINAPLUS~ to ensure proper tightening torque and a specific grease are crucial to ensure the durability and effectiveness of industrial tools.
If you are interested in a torque screwdriver to ensure the fixing of screws, contact us: www.sautool.com/en/contact-us
Due to its characteristics and advantages, DINAPLUS® has been chosen by the most important industries in the world.
Increase the competitiveness of your company.
SAU - Quality Tools Engineering since 1982.