La scelta dell’inserto ideale per la lavorazione di tornitura, è il primo passo per l’ottimizzazione del processo produttivo e si compie attraverso la valutazione di alcuni parametri di primaria importanza e di altri secondari, ma non per questo meno rilevanti. Vediamo insieme quali sono questi parametri.
- Profilo della lavorazione per la scelta della forma dell’inserto e angolo di attacco.
- Geometria dell’inserto in base al tipo di lavorazione, sgrossatura, media-finitura o finitura.
- Grandezza dell’inserto.
- Raggio di punta.
- Qualità del substrato e rivestimento.
Questi parametri vanno valutati assieme al materiale che si deve lavorare.
1 - Profilo della lavorazione e angolo di attacco
La figura in Tab.1 (sotto riportata), identifica la forma dell’inserto ideale in funzione al profilo da eseguire. La forma, abbinata alla Tab.2 che identifica l’angolo di attacco o di registrazione, influisce sulla formazione del truciolo.
Lo spessore del truciolo è direttamente proporzionale all’angolo di attacco: se aumenta l’angolo di attacco, aumenta di conseguenza lo spessore e la larghezza diminuisce. Questa condizione di taglio influisce anche sulla direzione del truciolo in uscita.
Tab.1
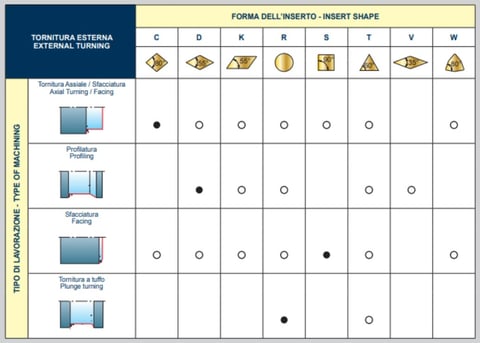
Tab.2
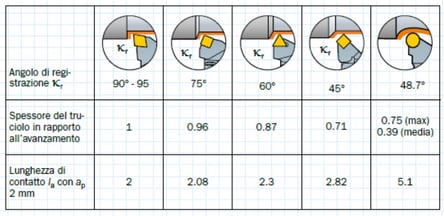
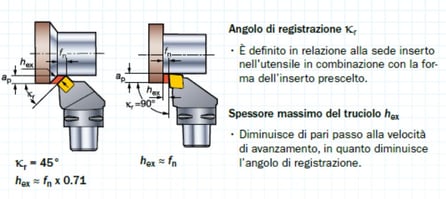
2 - Geometria dell'inserto
La geometria dell’inserto deve essere scelta in funzione della lavorazione, ovvero a seconda che si debba eseguire un'operazione di sgrossatura, media-finitura o finitura.
- SGROSSATURA: la robustezza del tagliente e il raggio di punta grande consentono profondità di taglio e avanzamenti elevati. Questo tipo di lavorazione richiede un'elevata forza di taglio.
- MEDIA-FINITURA: gli inserti per questo tipo di lavorazione sono i più utilizzati, in quanto consentono avanzamenti e profondità di taglio che spaziano dalla semi-sgrossatura alla semi-finitura.
- FINITURA: la preparazione del tagliente affilato e il raggio di punta adatto alla profondità di passata, garantiscono basse forze di taglio e buona finitura superficiale.
Per un controllo ottimale del truciolo, il campo di applicazione dell’inserto deve essere all’interno dei grafici riportati sul catalogo (vedi esempio Tab.3).
Tab.3
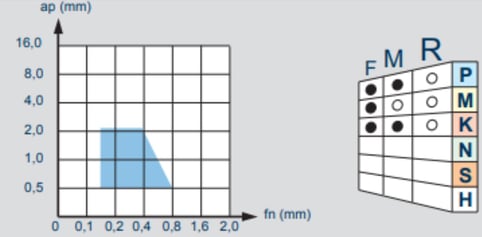
3 - Grandezza dell'inserto
Il tipo di lavorazione influisce anche sulla grandezza dell’inserto. Questo deve essere scelto in base alla profondità di passata “ap” e al tipo di inserto utilizzato.
Nella Tab.4 è riportata la linea guida per una corretta proporzione di robustezza del tagliente ed una economicità dell’inserto.
Tab.4
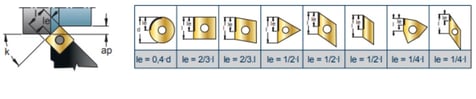
4 - Raggio di punta inserto
Altro fattore importante da valutare, spesso poco considerato, è il raggio di punta del tagliente. Per una corretta applicazione, generalmente questo non deve essere inferiore ai 2/3 della profondità di taglio “ap”. Inoltre, al raggio inserto si legano fattori come: la finitura superficiale, la formazione del truciolo e la resistenza del tagliente.
Normalmente il raggio piccolo ha un tagliente debole ed è utilizzato per lavorazioni di finitura con bassa profondità di taglio, là dove esistono problemi di vibrazioni ed un migliore controllo del truciolo.
Al contrario, il raggio grande è simbolo di robustezza del tagliente, grandi profondità di taglio ed elevati avanzamenti e ciò comporta maggiori forze di taglio e quindi rischio di vibrazioni.
Nella Tab.5 un estratto del catalogo SAU dove sono indicati gli avanzamenti massimi consigliati in funzione del raggio inserto e in via teorica approssimativa (ma sufficientemente affidabile), la rugosità che si ottiene in rapporto tra raggio inserto ”rɛ“ e avanzamento “fn”.
Tab.5
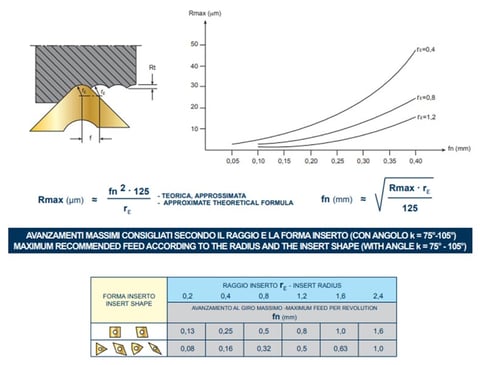
5 - Qualità substrato e rivestimento
Altri fattori che determinano la scelta dell’inserto da utilizzare per la lavorazione sono:
- materiale da lavorare (acciaio, inox, ghisa, non ferroso, lega resistente al calore, acciaio duro);
- stato del materiale (laminato, forgiato, stampato ecc.);
- tipo di lavorazione (sgrossatura, media, finitura);
- condizioni di lavoro (buone, medie, difficili).
Substrato o base del metallo duro, rivestimento con tecnologie PVD o CVD e geometria del tagliente, creano le combinazioni ideali per le lavorazioni da eseguire.
Nelle tabelle 6, 7, 8 e 9: la sequenza corretta per individuare l’inserto e i parametri di applicazione.
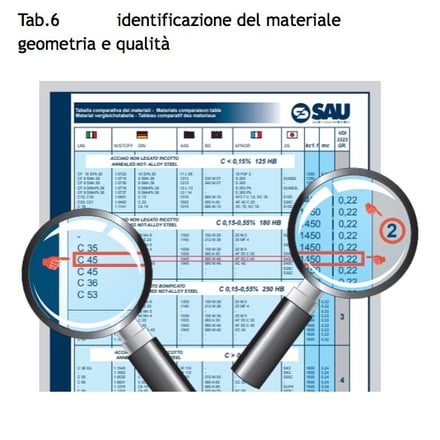
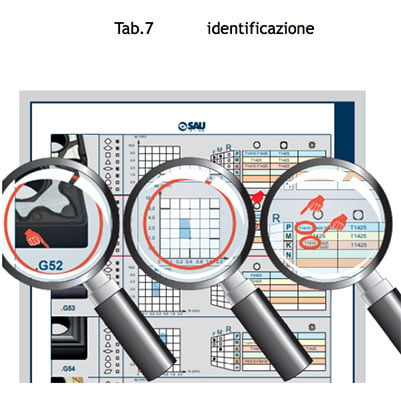
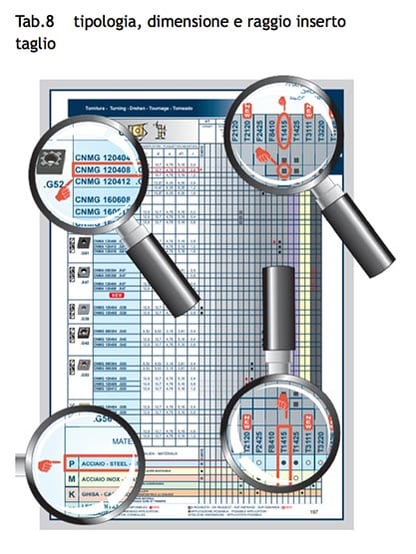